Cost-Effective Aluminum CNC Machining Solutions for Your Business
Selecting a reliable CNC machining partner is crucial for businesses seeking cost-effective aluminum machining solutions.

Aluminum CNC machining has become a popular choice for businesses looking to produce high-precision components efficiently. One of the key advantages of aluminum is its lightweight nature combined with excellent strength, making it ideal for various industries such as aerospace, automotive, and electronics. Furthermore, aluminum offers excellent corrosion resistance, ensuring durability and longevity for manufactured parts. These characteristics make aluminum CNC machining a cost-effective solution for businesses seeking high-performance materials at competitive costs.
Another benefit of aluminum CNC machining is its superior machinability. Compared to other metals like stainless steel or titanium, aluminum can be cut and shaped faster, reducing machining time and overall production costs. Additionally, aluminum dissipates heat efficiently, reducing the risk of tool wear and enabling higher cutting speeds. This leads to improved productivity and a reduction in material waste, making aluminum CNC machining an economical choice for businesses of all sizes.
Choosing the Right Aluminum Alloys for CNC Machining
Selecting the appropriate aluminum alloy is crucial to achieving cost-effective CNC machining solutions. Aluminum alloys come in various grades, each with distinct properties that suit different applications. For instance, 6061 aluminum is widely used due to its excellent mechanical properties and corrosion resistance, making it ideal for structural components and machine parts. On the other hand, 7075 aluminum is known for its exceptional strength and hardness, often utilized in aerospace and high-performance applications.
Choosing the right alloy helps businesses balance performance and cost efficiency. For companies looking for a budget-friendly option without compromising quality, 5052 aluminum can be a great choice due to its good corrosion resistance and moderate strength. Understanding the characteristics of different aluminum grades allows manufacturers to optimize material selection, reducing unnecessary costs while maintaining the required performance standards.
Cost-Reduction Strategies in Aluminum CNC Machining
Reducing manufacturing costs without sacrificing quality is a top priority for businesses utilizing aluminum CNC machining. One of the most effective strategies is optimizing the design of the parts to minimize material waste. By employing design-for-manufacturing (DFM) principles, engineers can create parts that require fewer machining steps, reducing production time and tool wear. Additionally, using CAD/CAM software allows manufacturers to refine designs and simulate machining processes, identifying potential inefficiencies before production begins.
Another cost-saving approach is batch production. Ordering aluminum CNC machined parts in bulk can significantly lower per-unit costs due to economies of scale. Many machining service providers offer volume discounts, helping businesses save money on large orders. Furthermore, partnering with reliable CNC machining suppliers that use automated and high-speed machining techniques can lead to cost savings by reducing labor costs and increasing overall efficiency.
Leveraging Advanced CNC Machining Technologies for Efficiency
Incorporating advanced CNC machining technologies can further enhance cost efficiency in aluminum machining. High-speed machining (HSM) techniques enable manufacturers to produce complex parts with greater accuracy and faster cycle times. By using multi-axis CNC machines, businesses can reduce the number of setups required, minimizing downtime and improving production speed. Automated tool changers and adaptive machining strategies also contribute to cost savings by ensuring seamless and efficient machining operations.
Another technological advancement that improves cost-effectiveness is the use of CNC machining centers equipped with real-time monitoring systems. These systems track machining parameters and tool wear, allowing for proactive maintenance and reducing unexpected downtimes. By leveraging smart machining solutions, businesses can enhance productivity, optimize resource utilization, and ultimately lower their aluminum CNC machining costs.
Finding the Right CNC Machining Partner for Your Business
Selecting a reliable CNC machining partner is crucial for businesses seeking cost-effective aluminum machining solutions. A reputable machining provider should have extensive experience in aluminum CNC machining and access to advanced machinery and technology. Checking customer reviews, past projects, and certifications can help businesses evaluate potential suppliers and ensure they meet quality standards.
Additionally, businesses should consider the geographical location of their CNC machining partner. Sourcing from local suppliers can reduce shipping costs and lead times, improving overall cost efficiency. Establishing a long-term partnership with a trusted machining provider can also lead to better pricing, faster turnaround times, and enhanced product quality. By carefully selecting a CNC machining partner, businesses can maximize the benefits of aluminum CNC machining while keeping costs under control.
What's Your Reaction?
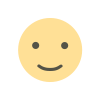





