The Future Landscape of Injection Molding
Explore injection molding techniques, materials, and their diverse applications in the manufacturing industry.

Injection molding is an essential manufacturing technique that shapes raw plastic into finished components. This method is known for its precision, efficiency, and adaptability, making it a top choice across various sectors. In this comprehensive article, we will delve into the details of injection molding, including its techniques, materials, and applications, all while ensuring optimal SEO practices.
Defining Injection Molding
Injection molding is a production process that involves injecting molten material into a mold to create parts. This technique is particularly favored for producing plastic components due to its ability to achieve high accuracy and complex shapes.
Key Characteristics of Injection Molding
- Efficiency: After the mold is created, the production cycle can be incredibly fast, allowing manufacturers to produce large quantities of parts quickly.
- Complex Shapes: This method can create intricate designs that are often challenging to achieve with other manufacturing processes.
- Material Flexibility: Injection molding accommodates a wide range of materials, including both thermoplastics and thermosets.
Various Injection Molding Techniques
Several techniques exist within the realm of injection molding, each tailored for specific materials and applications.
1. Standard Injection Molding
This is the most prevalent form of injection molding, where molten plastic is injected into a mold under high pressure.
2. Gas-Assisted Injection Molding
In this method, gas is introduced into the mold to form hollow parts, which helps reduce material usage and weight.
3. Multi-Shot Injection Molding
This technique allows for the injection of multiple materials into a single mold, enabling the creation of multi-colored or multi-material components.
4. Insert Molding
Insert molding integrates metal or other materials during the injection process, adding strength and functionality to the final product.
5. Blow Molding
While distinct, blow molding is often discussed alongside injection molding. It primarily produces hollow plastic parts, such as bottles.
Materials Commonly Used in Injection Molding
Selecting the right material is crucial, as it influences the properties of the final product. Here are some commonly utilized materials:
Thermoplastics
- Polycarbonate: Renowned for its strength and clarity, polycarbonate is perfect for applications that demand durability and transparency.
- ABS (Acrylonitrile Butadiene Styrene): This versatile material is tough and widely used in consumer goods and automotive parts.
- Polypropylene: Lightweight and resistant to chemicals, polypropylene is often found in packaging and automotive applications.
Thermosets
- Epoxy Resins: These materials exhibit excellent adhesion and heat resistance, making them suitable for electrical components.
- Phenolic Resins: Known for their high thermal stability, phenolic resins are frequently used in fire-resistant applications.
Benefits of Injection Molding
Injection molding presents numerous advantages, making it a preferred option for manufacturers.
1. Cost-Effectiveness
After the initial mold is established, producing large volumes of parts becomes economically viable, significantly lowering the cost per unit.
2. Consistency and Precision
The process ensures high precision, guaranteeing that each component meets stringent specifications. This consistency is vital in sectors like automotive and medical.
3. Minimal Waste
Injection molding significantly reduces material waste, as excess materials can often be recycled or reused.
4. Quick Production Rates
One of the process's most notable benefits is its rapid production capabilities, allowing companies to meet tight deadlines effectively.
Injection Molding Applications
Injection molding finds use in various industries, showcasing its versatility. Here are some key applications:
1. Automotive Sector
Injection molding is integral to producing components such as dashboards, bumpers, and interior fittings.
2. Consumer Goods
From toys to kitchen utensils, many everyday items are manufactured using injection molding, thanks to its efficiency and cost-effectiveness.
3. Medical Equipment
The medical field relies on injection molding to create components like syringes, surgical tools, and device housings.
4. Electronics
This method is essential for producing casings and components for electronic devices, ensuring both durability and precision.
5. Packaging Solutions
Many packaging products, including containers and closures, are made using injection molding techniques.
The Future Landscape of Injection Molding
As technology advances, the injection molding industry continues to evolve. Here are some trends shaping its future:
1. Automation and Robotics
Integrating automation into the injection molding process boosts efficiency and reduces labor costs.
2. Sustainable Manufacturing Practices
Manufacturers are increasingly adopting sustainable approaches, exploring eco-friendly materials and methods to lessen their environmental footprint.
3. Innovative Materials
The emergence of new materials, including bioplastics, is broadening the horizons of what injection molding can achieve.
Conclusion
Injection molding stands as a cornerstone of contemporary manufacturing, offering unmatched efficiency, precision, and adaptability. From automotive components to medical devices, its applications are extensive and diverse. As the industry progresses, embracing technological advancements and sustainable practices will be crucial for ongoing success.
For further insights into injection molding solutions, check out resources on China injection molding and learn about plastic mold manufacturing.
What's Your Reaction?
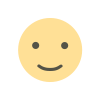





